YOUR REQUIREMENTS,
OUR PRECISION
We are your partner for first-class roller surfaces in the metal industry. Since 1989 we have been supplying innovative solutions for the highest demands on rollers for steel, aluminum, copper and brass. As a joint venture between thyssenkrupp steel europe AG and Court Holdings Ltd, Canada, we set standards in quality and precision.
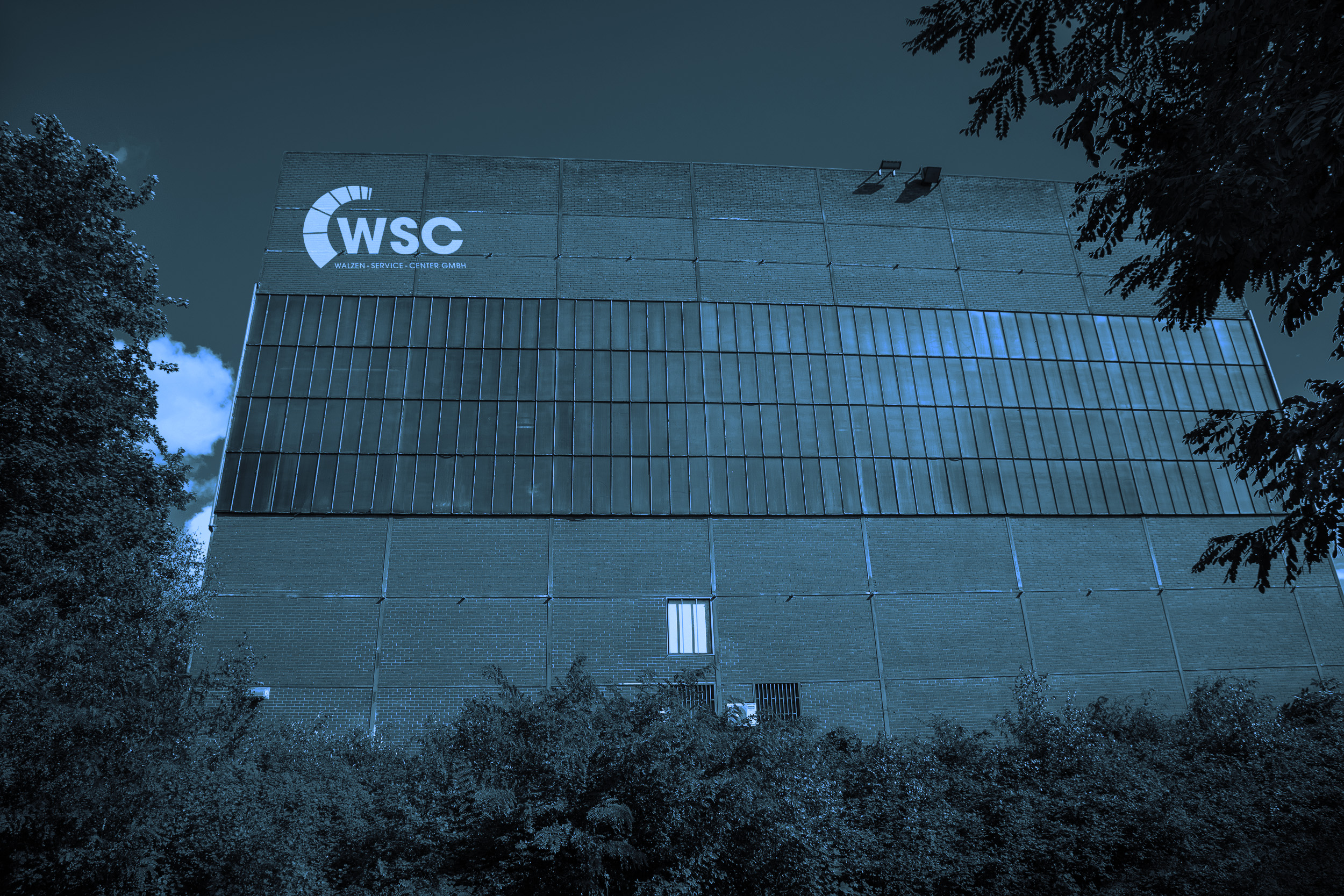
WHO WE ARE
Since 1989 we have stood for top performance in roll surfaces for the metal industry. As a joint venture of thyssenkrupp steel europe AG and Court Holdings Ltd., Canada, we have made it our business to equip cylinders for steel, aluminum, copper and brass with the highest precision and quality.
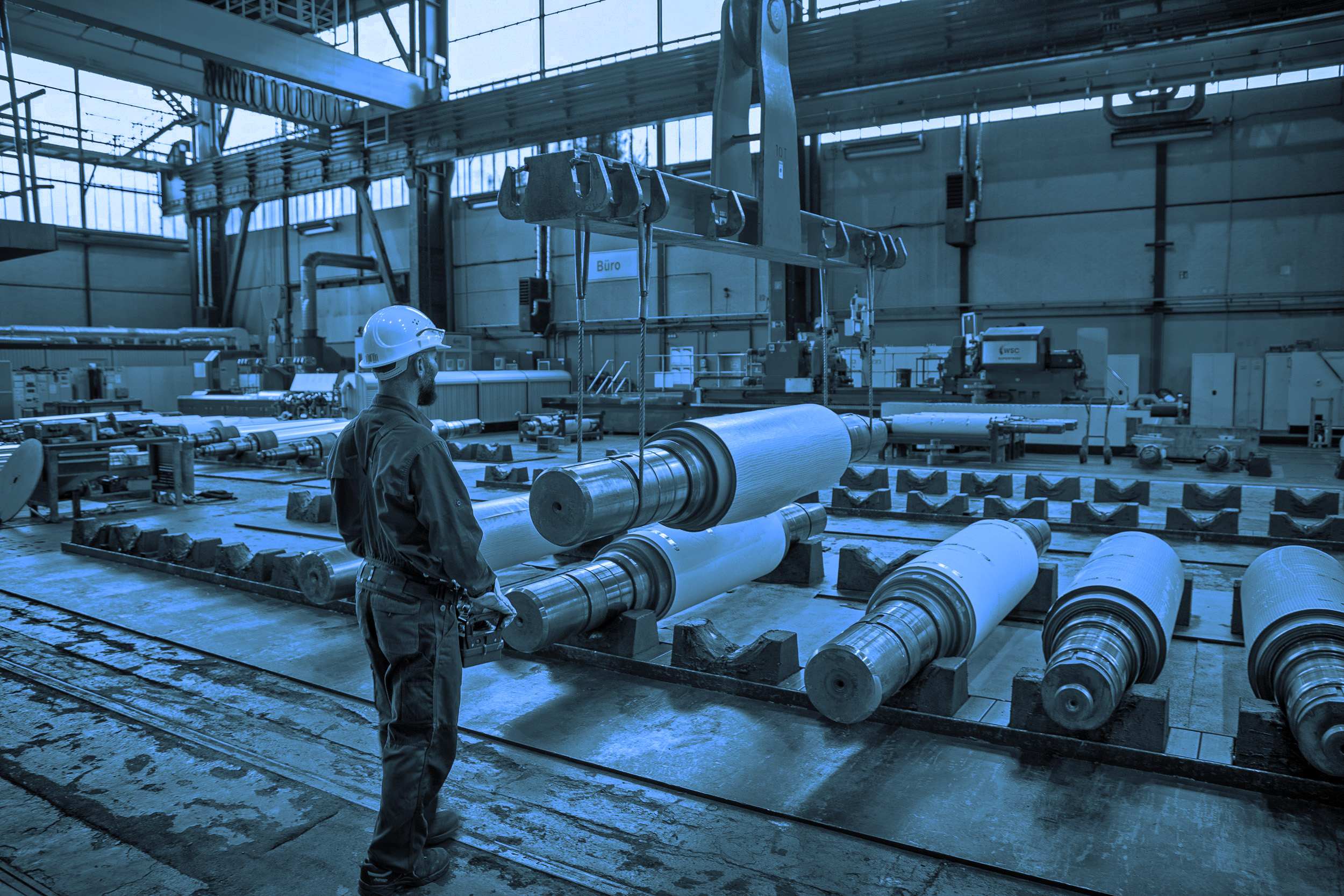
OUR MISSION
Durability, productivity and precision for your processes. Using state-of-the-art processes such as electro-discharge texturing and hard chrome plating, we develop surfaces that guarantee both maximum resilience and optimum processing properties. Our locations in Oberhausen and Dortmund stand for efficiency and proximity to our customers.
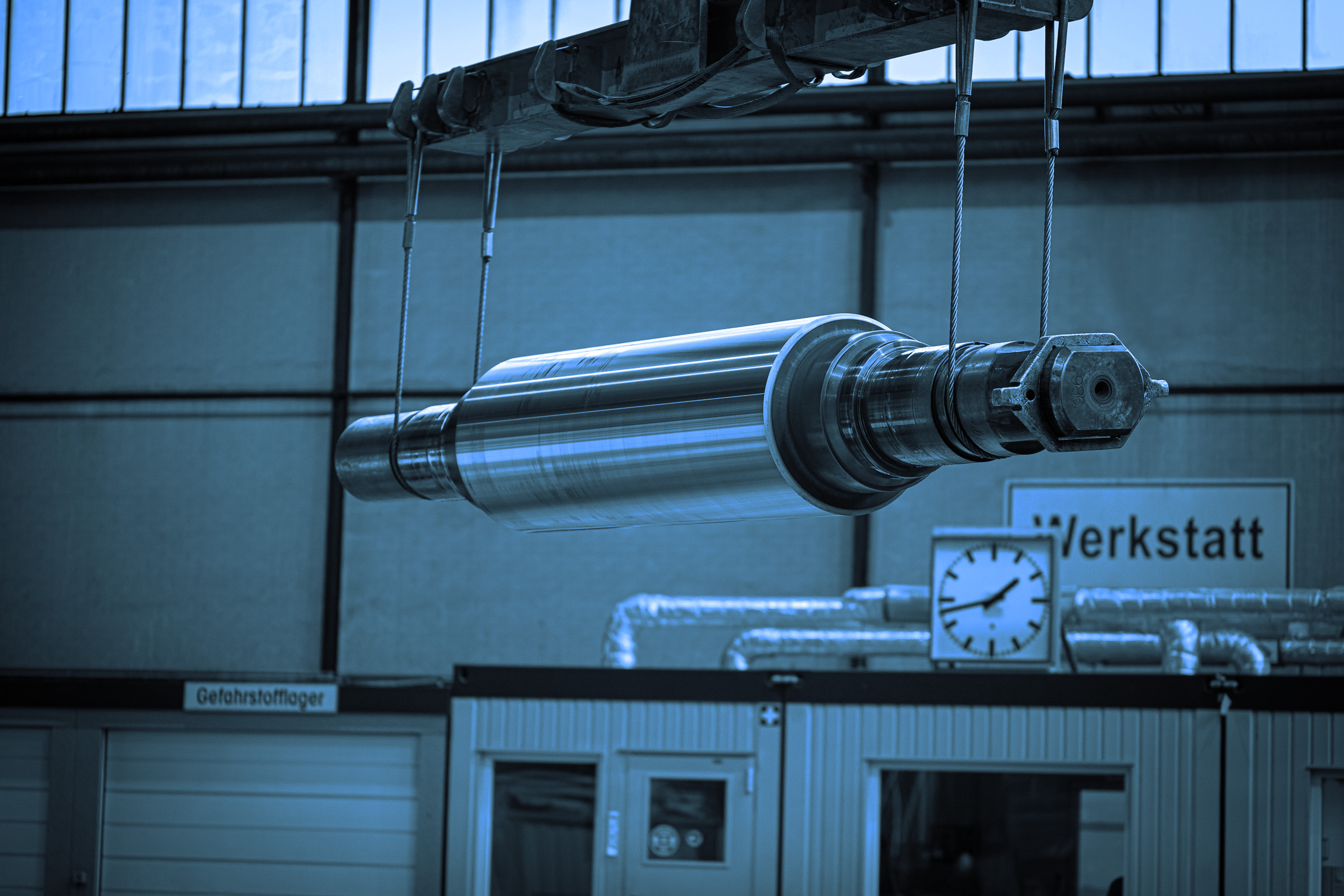
OUR GUIDELINES
Innovation and quality characterize our actions. By constantly investing in technology and expertise, we remain a reliable partner that will continue to meet the highest standards in the future. Together we create surfaces that set standards.
ROLLER FINISHING SINCE 1989
# Elektro-Discharge-Texturierung
# Superfinish™
# Hartverchromung
PERFORMANCE
ADVANTAGES
REDUCTION IN PRODUCTION COSTS
UP TO THREE TIMES LONGER SERVICE LIFE OF THE ROLLERS IN THE STAND, LOWER SET-UP AND GRINDING COSTS, LONGER ROLLER SERVICE LIFE AND MINIMIZATION OF THE ROLLER FLEET.
SURFACE VARIETY
SURFACE ROUGHNESSES FROM 1-16µm RA WITH DIFFERENT RPCS FOR EACH ROUGHNESS, ADAPTED TO THE DIFFERENT SURFACE REQUIREMENTS AND ROLLING CONDITIONS OF OUR CUSTOMERS.
FLEXIBILITY
SHORT-TERM PROCESSING OF CUSTOMER INQUIRIES, PROVISION OF CAPACITIES FOR TEST SERIES, AS WELL AS THEIR ACCOMPANIMENT IN OUR FACTORY. SHORT PROCESSING TIMES FROM DELIVERY TO COLLECTION.
PROCESS
STEP 1
MAKING CONTACT
- You send us your contact
- We get in touch with you
STEP 2
COLLABORATION
- Free advice on optimal roller machining
- Preparation of quotation
- Coordination of logistics and deadlines
CONTACT US
WE LOOK FORWARD TO HEARING FROM YOU!
- Essener Straße 259 // 46047 Oberhausen
PERFORMANCE
ELECTRO-DISCHARGE TEXTURING
Electro-discharge texturing (EDT) is a spark erosion process for shaping the surface structure of work rolls in the cold rolling industry. It determines the surface quality of the rolled material such as steel, aluminum, copper and brass. By using different electrode materials, polarities and modes, we achieve uniform surface roughness of 1 to 16 μm Ra over the entire roll length. 1 bis 16 μm Ra über die gesamte Walzenlänge.
Ra = 1,8 μm; EDT cap(-); HV
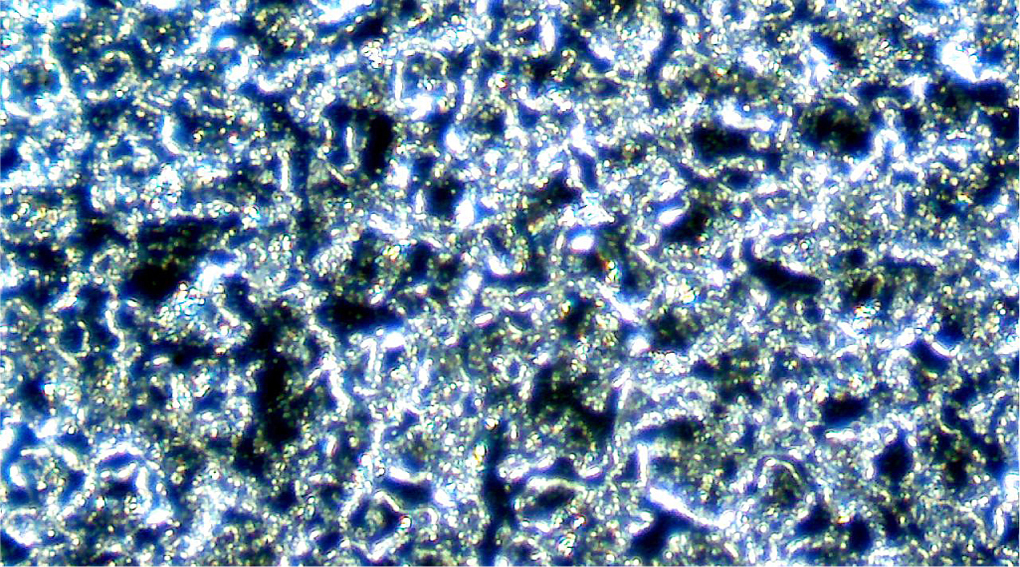
Ra = 2,3 μm; EDT graphit; SF; HV
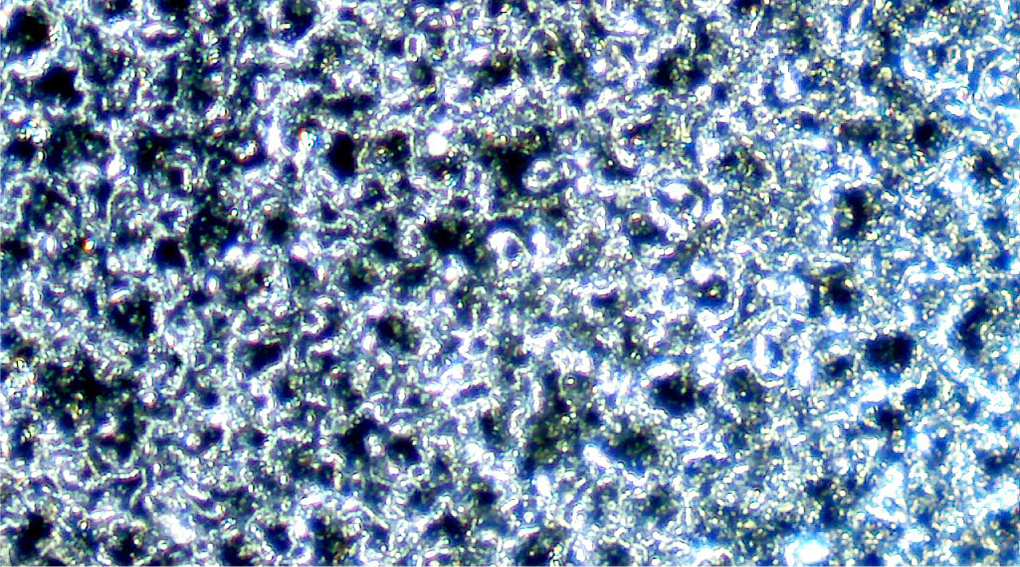
Ra = 3,0 μm; EDT puls(+);SF; HV
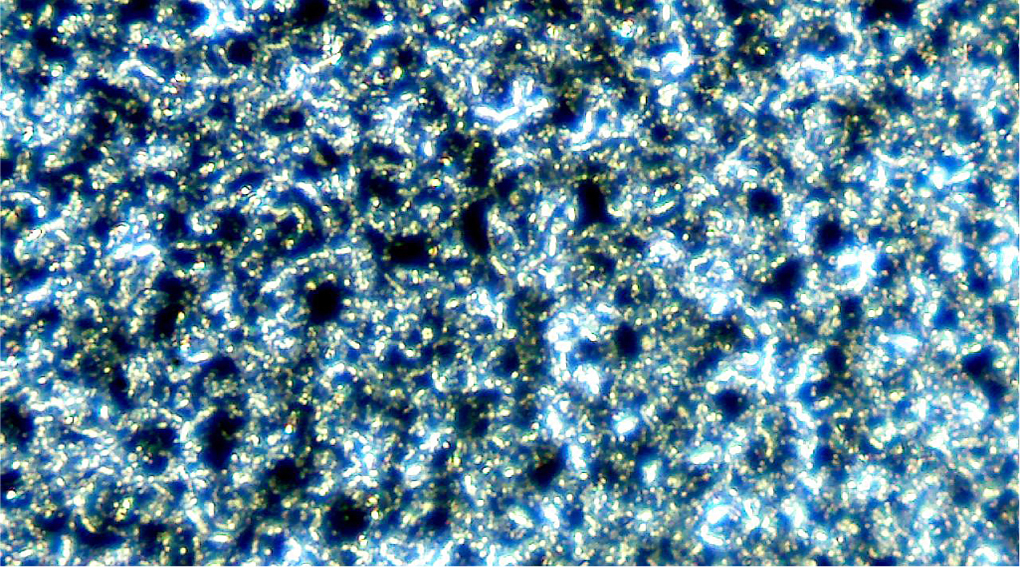
SUPERFINISH (SF)
Superfinish (SF) is a finishing technique that is applied after the EDT process to further optimize the surface structure of work rolls. The profile peaks are removed by precise belt grinding, resulting in a uniform roughness structure and a significant increase in the contact ratio. This technology improves the load distribution of the rollers and reduces wear in the rolling process. Superfinish rolls impress with their extended service life in the roll stand and guarantee a consistent surface quality of the rolled products.
ROLLER SURFACE WITH TEXTURING
TEXTURING + SUPERFINISH
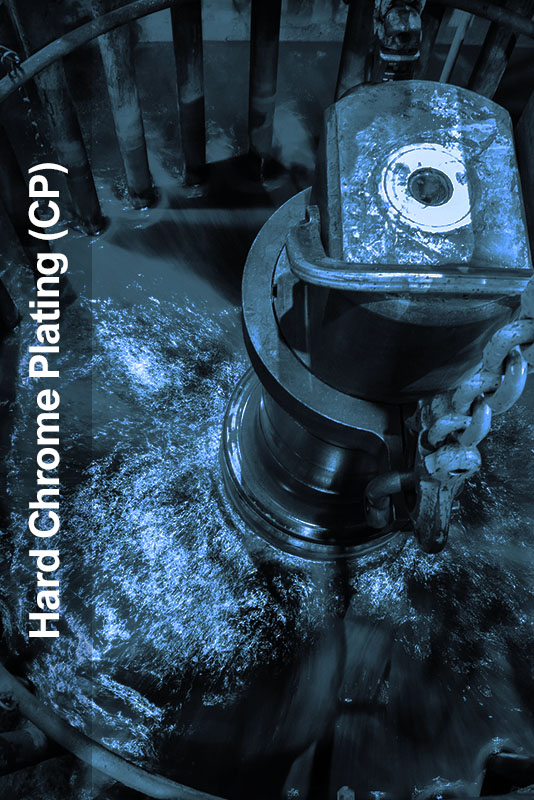
HARD CHROME PLATING
By immersing the rollers in a chromic acid bath and applying direct current (anode +, roller -), a thin chromium layer of a few micrometers is applied, which permanently preserves the fine surface structure of the rollers. This chrome layer minimizes the adhesion of strip abrasion during the rolling process and at the same time improves thermal conductivity. The result: consistent surface quality of the rolled products and up to three times longer roll service life.
TOP VIEW AND CROSS-SECTION OF A CHROME LAYER FINE STRUCTURE
MICROCRACKS OF A CHROME-PLATED SURFACE
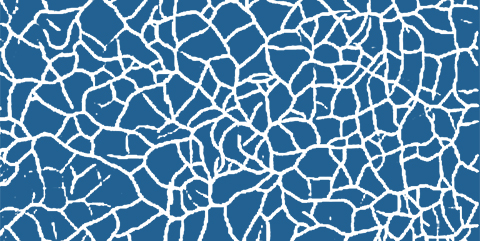
MICROCRACKS ETCHED, MAGNIFIED 500X
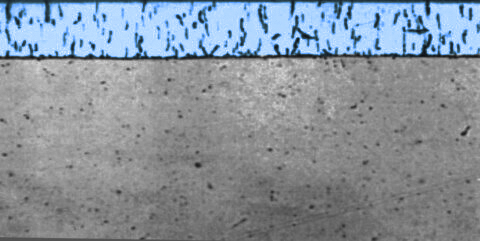
LASER TEXTURING
Laser microstructuring with ultrashort pulse lasers is a new technology for applying surface textures with very fine features and an extremely high depth resolution. It enables the creation of small-scale textures that change the functional properties of surfaces, e.g. reducing friction or changing optical properties. With ultrashort laser pulses, the energy is emitted in such a short time that ablation takes place before heat conduction into the base material. Therefore, ultrashort laser pulses can be used to process materials without thermally affecting the surrounding material. This enables more precise processing of materials with significantly fewer negative heat-related effects. The laser beam with high energy and high repetition frequency is focused on the roller surface to form a micro-melt pool; the micro-convex concave body is formed under the action of side-blast gas and centrifugal force, and the texturing lattice with high hardness is obtained by ultra-fast cooling. As a result, the roller after texturing can have high surface hardness, controllable shape and long service life, and improve the production efficiency of the rolling mill. The random signal is used to randomly change the morphology and arrangement of the textured points, so that the surface has a disordered, holey surface structure. Scope of application: it is used in steel, aluminum, titanium and other industries. It meets the texturing requirements of cold rolling and texturing of various work rolls, such as temper mill, finisher, rolling mill and tandem mill.
HIGHEST QUALITY STANDARDS
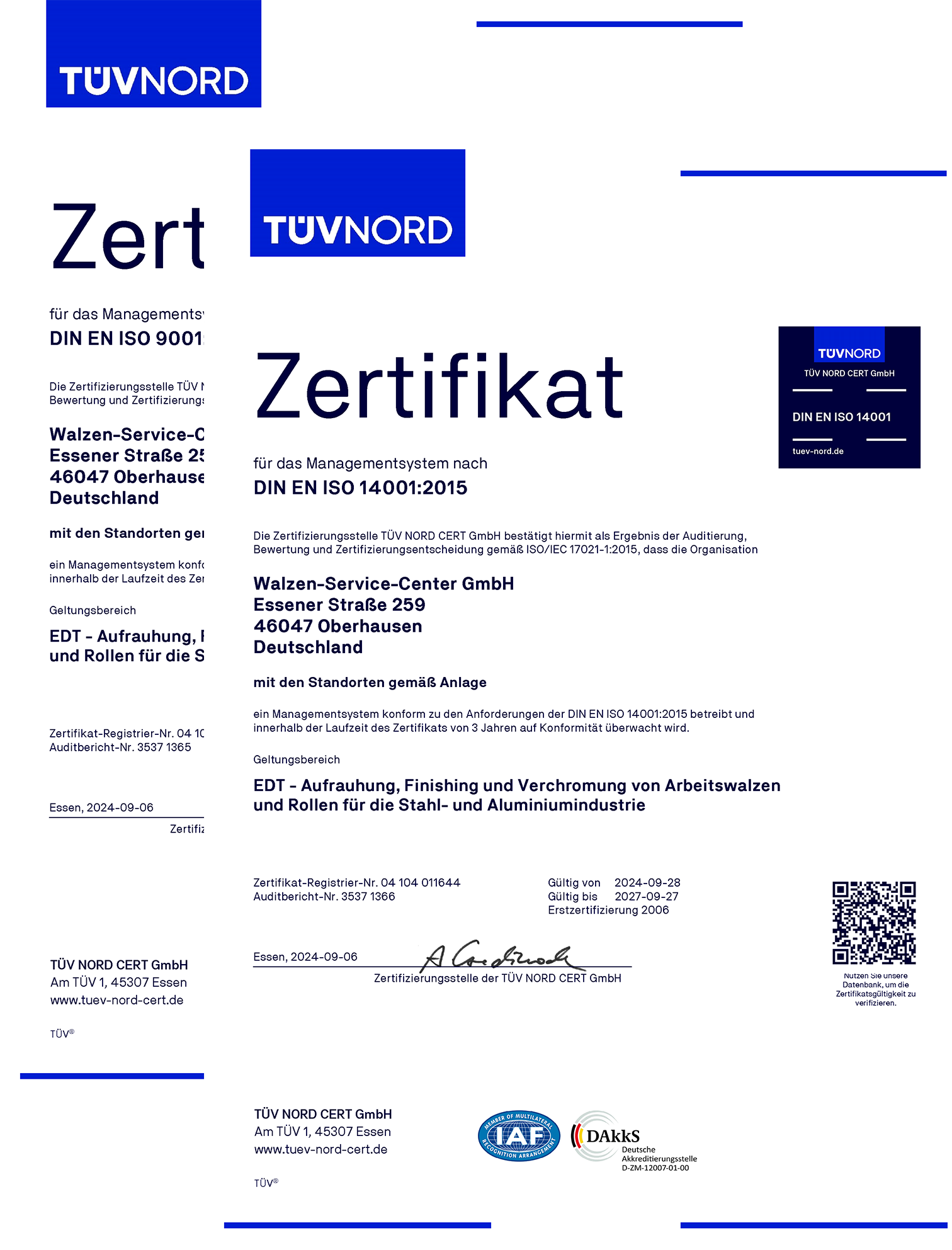
WALZEN-SERVICE-CENTER GMBH
LOCATIONS
OBERHAUSEN
- Essener Straße 259 · 46047 Oberhausen
DORTMUND
- Rüschebrinkstraße · 44145 Dortmund
OUR CUSTOMERS
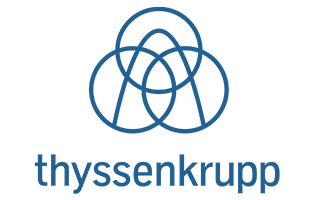
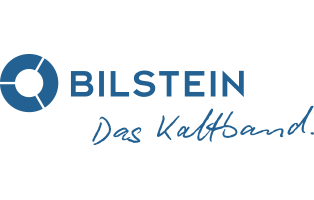
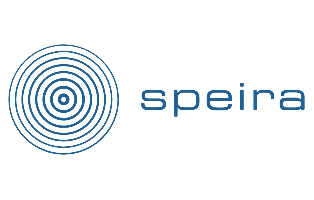
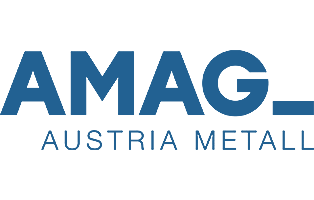
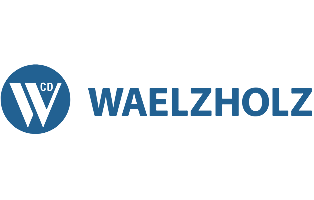
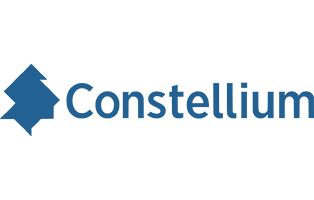
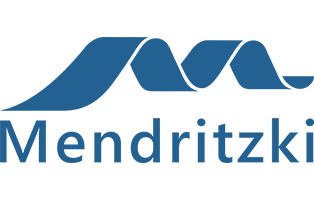
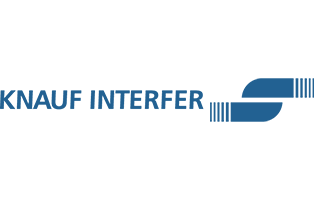
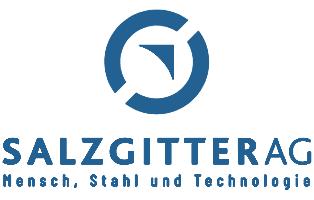
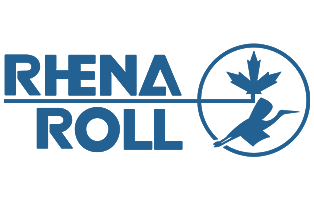
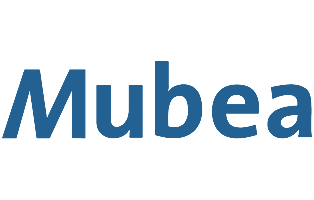
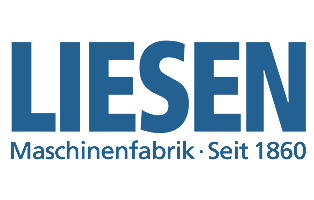
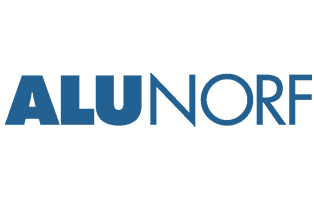
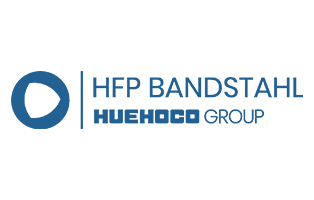
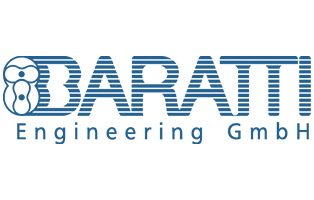
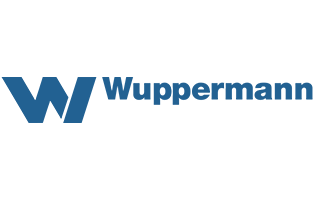
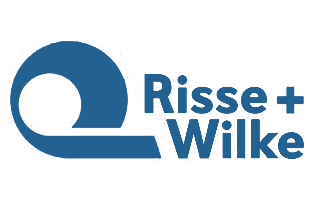
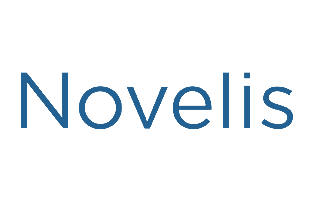
